Mastering the Art of Welding: Just How to Avoid Undercut Welding Issues for Flawless Manufacture Outcomes
Performance and precision are vital on the planet of welding, where even the least imperfection can compromise the architectural stability of a made item. One typical obstacle that welders face is undercutting, a problem that can lead and compromise a weld joint to expensive rework. By recognizing the root triggers of undercut welding and applying effective techniques to avoid it, welders can boost their craft to new degrees of excellence (Preventing weld undercut). In the quest of perfect manufacture outcomes, mastering the art of welding to prevent undercut concerns is not just a skill however a requirement for those pursuing excellence in their work.
Understanding Undercut Welding

To protect against undercut welding, welders ought to make certain appropriate welding criteria, such as adjusting the current, voltage, travel rate, and keeping the proper electrode angle. By understanding the causes of undercut welding and applying precautionary procedures, welders can accomplish high-quality, structurally audio welds.
Sources Of Undercut in Welding
Understanding the aspects that contribute to undercut in welding is essential for welders to produce top notch, structurally audio welds. Poor welding inaccurate or existing welding speed can likewise contribute to undercut. Comprehending these reasons and implementing appropriate welding methods can help prevent damaging concerns, making certain resilient and solid welds.
Techniques to Protect Against Undercutting

To minimize the risk of damaging in welding, welders can employ calculated welding strategies intended at improving the high quality and honesty of the weld joints. One reliable approach is to change the welding parameters, such as voltage, existing, and take a trip rate, to make certain correct warm input and deposition. Preserving an ideal electrode angle and making sure constant traveling rate can also help protect against undercut. Furthermore, making use of the proper welding technique for the specific joint setup, such as weave or stringer grains, can add to lowering undercutting. Preventing weld undercut.
Utilizing back-step welding methods and managing the weld grain account can also help distribute heat evenly and decrease the risk of undercut. Normal directory evaluation of the weld joint during and after welding, as well as carrying out quality assurance steps, can help in detecting and dealing with undercutting problems immediately.
Value of Appropriate Welding Parameters
Selecting and keeping suitable welding criteria is necessary for attaining effective welds with very little issues. Welding criteria describe variables such as voltage, existing, take a trip speed, electrode angle, and securing gas circulation price that straight influence the welding process. These specifications must be thoroughly adjusted based on the kind of material being welded, its density, and the welding technique used.
Appropriate welding criteria make certain the correct amount of heat is put on thaw the base metals and filler material uniformly. If the criteria are set too expensive, it can lead to too much warm input, creating spatter, distortion, or burn-through. On the other hand, if the parameters are as well reduced, insufficient fusion, lack of penetration, or damaging may happen.
High Quality Assurance in Welding Procedures
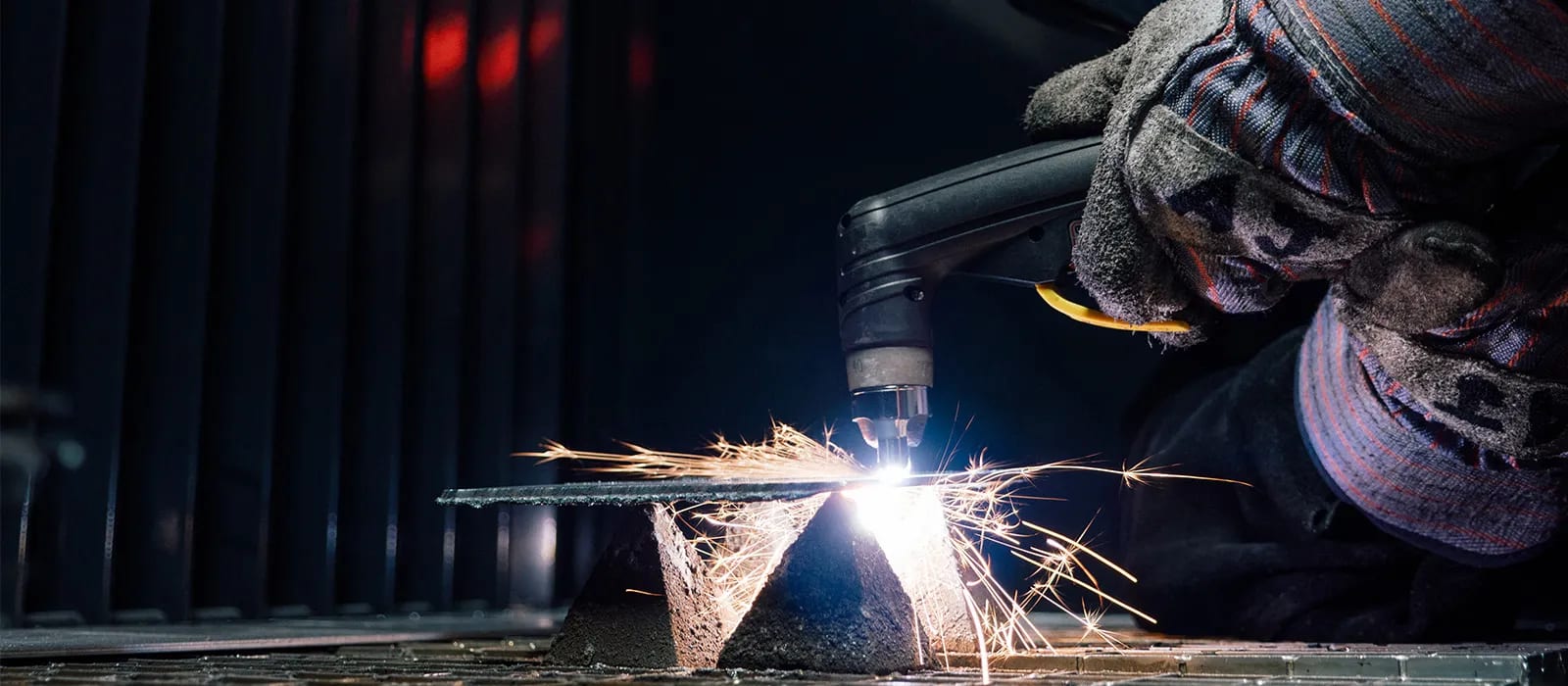
Final Thought
To conclude, mastering the art of welding calls for a thorough understanding of undercut welding, its reasons, and methods to stop it. By making why not check here certain appropriate welding parameters and applying quality control techniques, perfect construction results can be attained. It is vital for welders to regularly pursue excellence in their welding operations to avoid undercut issues and create top notch welds.
Undercut welding, a common flaw in welding processes, takes place when the weld metal does not correctly load the groove and leaves a groove or depression along this website the bonded joint.To stop undercut welding, welders should make sure proper welding specifications, such as readjusting the present, voltage, traveling rate, and keeping the correct electrode angle. Poor welding present or wrong welding rate can also add to undercut.To alleviate the threat of damaging in welding, welders can use calculated welding techniques intended at boosting the quality and stability of the weld joints.In verdict, understanding the art of welding calls for an extensive understanding of undercut welding, its reasons, and strategies to stop it.